
フジワラの強み
長年の航空機部品製造で培ったオンリーワンの技術が
信頼性
特殊工程認定
弊社で作られる複合材製品の各工程は顧客スペック(仕様書)で特殊工程としての管理が要求されており、成形作業者及び検査員の力量等を管理し、技術、技能の維持向上のため社内認定制度を設けています。社内認定制度は国内航空機メーカー及び外部認証機関からQMS(品質マネジメントシステム)の認証を受けています。
外部認証機関の認証
航空宇宙産業における国際特殊工程認定制度であるNadcapやMIL規格等の認証を取得し、航空機製品に定められた品質保証能力を維持しております。(1998年にJIS Q 9001、2004年にJIS Q 9100、2007年にNadcapComposites及びNon DestructiveTestingの認証を取得し、維持しています。)
非破壊検査員認証
複合材部品の内部欠陥を検出するため、非破壊検査員認証(NonDestructive Inspection :以下NDI)を実施し製品品質を保証します。NDI検査員の国際認定システム要求であるNAS410に基づき(NDI)検査員を認定し、NAS410システムによる技能レベル3の検査員を育成・管理しております。豊富な経験・知識を保有した検査員による非破壊検査を実施し判定を行っており、信頼性の高い複合材製品を提供いたします。
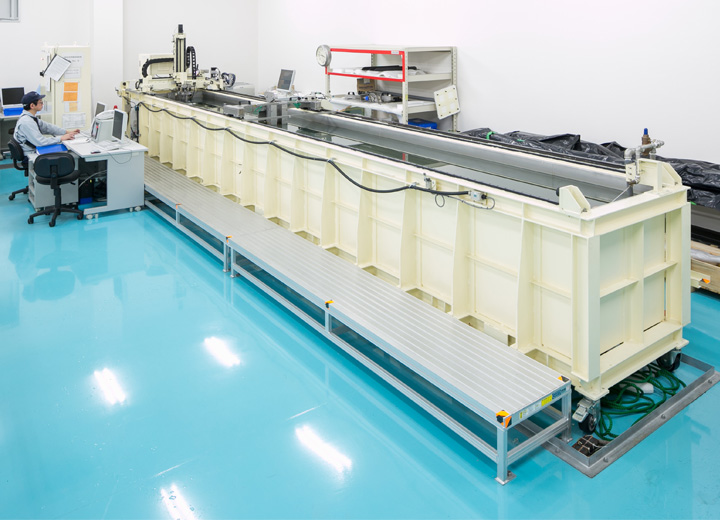
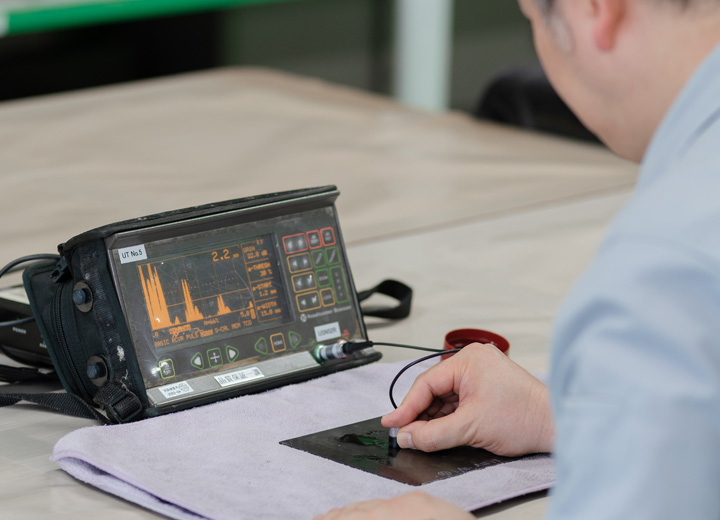
超音波探傷検査装置
トレーサビリティ
徹底した材料・工程記録管理で使用した材料や作業日時を追跡することが可能です。
航空機は少しでも不具合があると即、重大な事故につながってしまうため、製品が図面やスペック指示通り確実に実施したか分かるように全ての製造工程において記録を取り、いつ、誰が、どの部品の、どの工程を作業したのか分かるようになっています。また、使用した材料においても、どの部品にどの材料が使用されたか確実に記録を残しております。
精密性
研磨精度
熟練の職人技による研磨技能で数μm単位の精度で研磨を行い、歪の無いアクリル・ポリカーボネートを提供することが可能です。
光学歪みの大きさは、入射角、パネルの曲率の変化、板厚、表面の凹凸等の要因によって決まりますが、表面研磨によって光学歪みの軽減が可能です。研磨方法は各種研磨材を用いて、高い力量を持っている熟練者の研磨技能により、歪や傷を除去し、高い光学特性を実現しています。
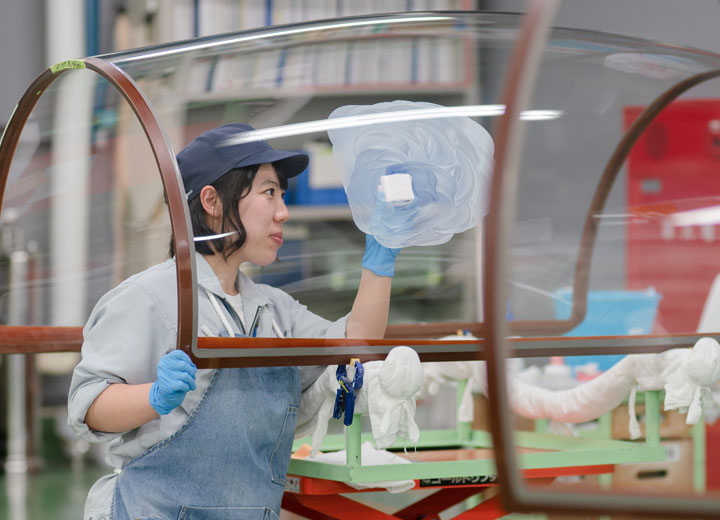
研磨作業
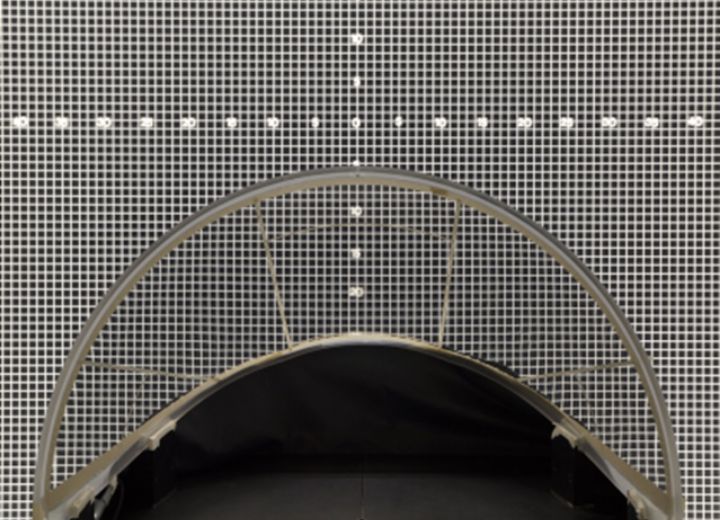
グリッドボード試験
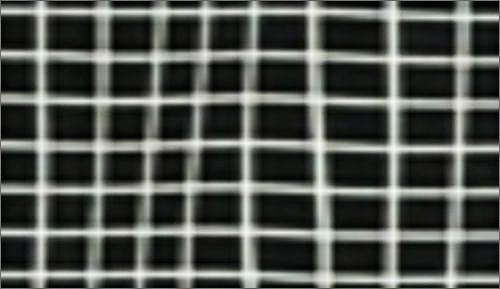
研磨前
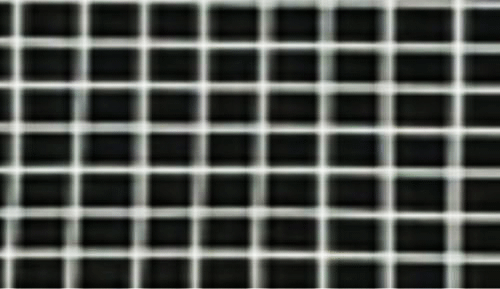
研磨後
ライティングパネルの調光精度
アクリルの導光性を活かしたライティングパネルでは、下地の白塗装の濃淡による輝度・色度を作業者の経験による調光技能で、同じ明るさにすることができます。光輝した文字等の輝度を確認し、光の色を測定しながら調光していきます。
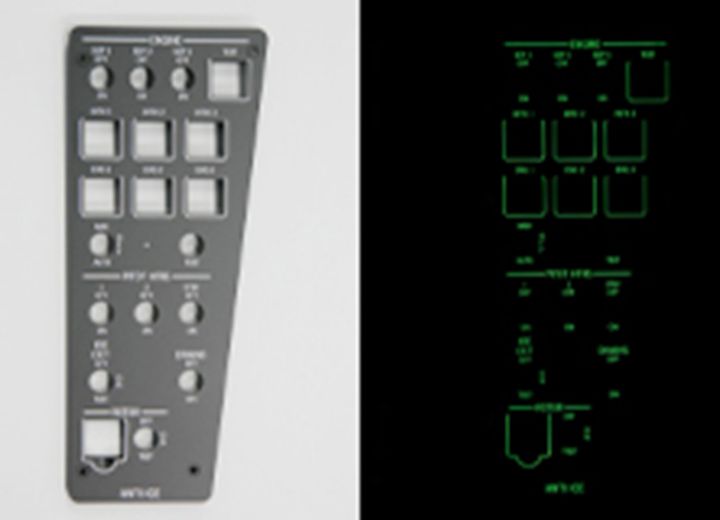
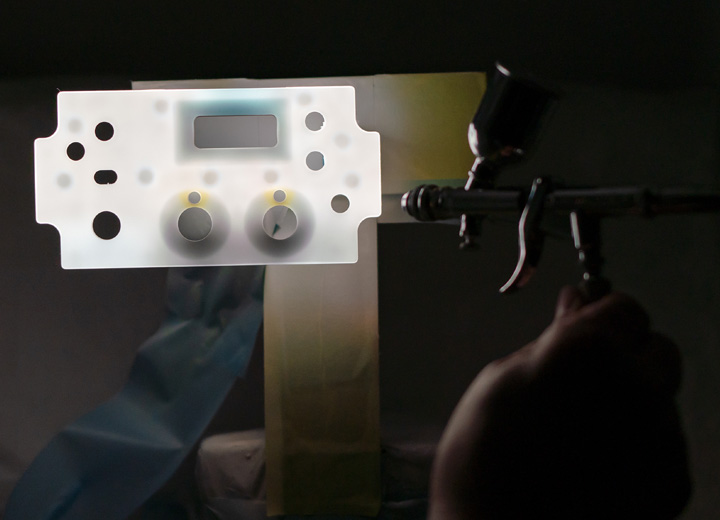
輝度測定作業
高い寸法精度
航空機の高い寸法精度に対応しております。
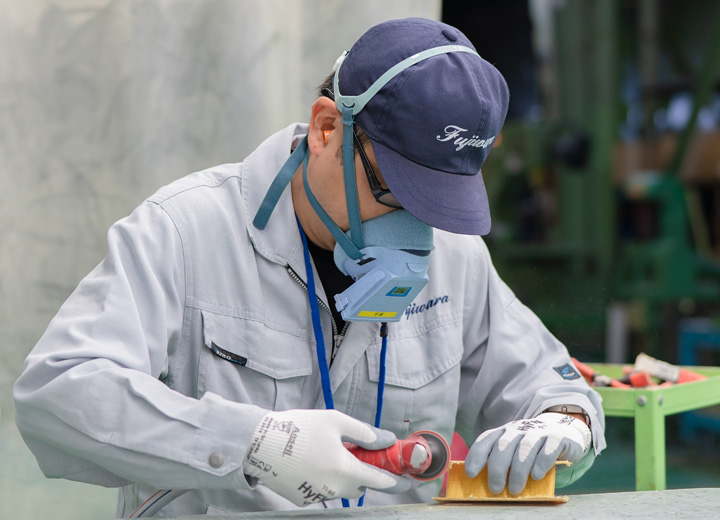
異物ゼロの成形精度
複合材料は繊維方向以外に受ける外力に弱い為、層間剥離を生じた素材では圧縮強度が著しく低下してしまいます。そのため層間剥離の原因となる異物の混入を徹底的に防止し、高強度の部品を製作しています。
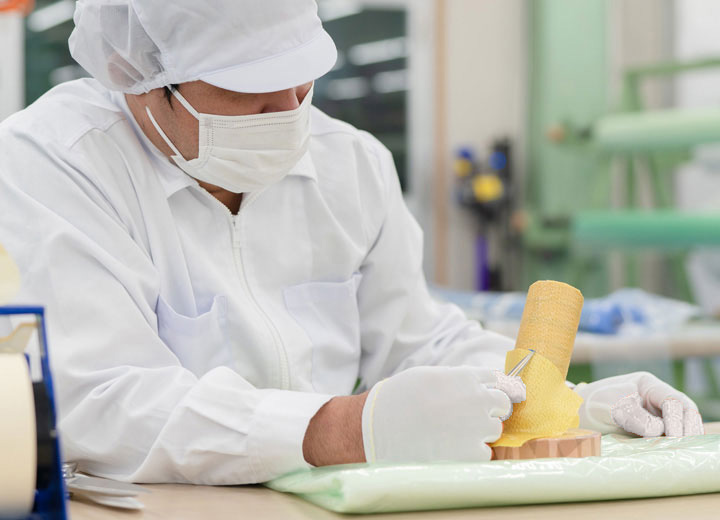
技術力
複合材部品の軽量化技術
ハニカムコアや発泡コアをCFRPスキンで挟み込んだサンドイッチパネル構造により製品の軽量化を実現します。複雑な曲面にも対応可能です。
複合材部品の接着技術
複合材部品とハニカムコアやロハセル等の材料をフィルム接着材で接着し、一体成形加工することで高強度で軽量の部品を製作することが可能です。また、2液性接着剤も取り扱っており、用途に合わせた複合材部品との接着が可能です。
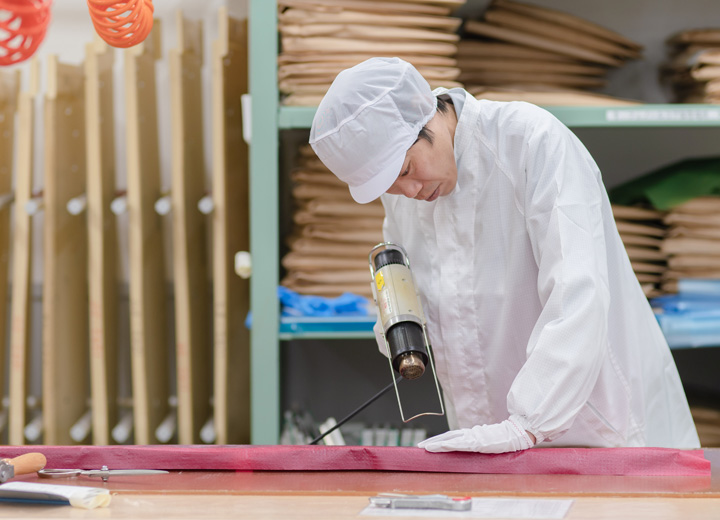
フィラメント・ワインディング(FW)成形技術
FWマシンによる自動巻き付けで材料の繊維方向やピッチをコントロールし、高強度のパイプ状部品の製作が可能です。
樹脂を含浸させた炭素繊維を金型に自動巻付けした後、加熱硬化して製品を得る成形法です。形状は回転体に限られますが、繊維含有率の高い安定した品質が得られます。
- 円筒高圧タンクや、高強度角柱パイプ構造の製造実績あり
- 圧力容器の最適設計/成形/試験評価技術を保有
- 4軸駆動装置で複雑な巻きパターンに対応
- 6m×φ1mの製品まで対応
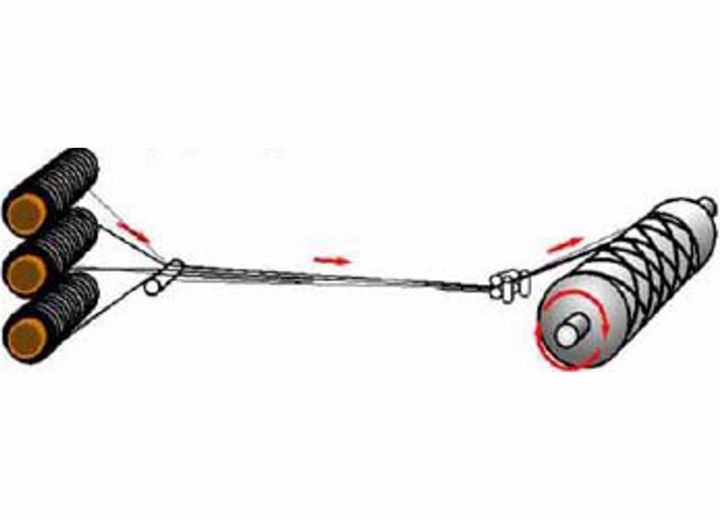
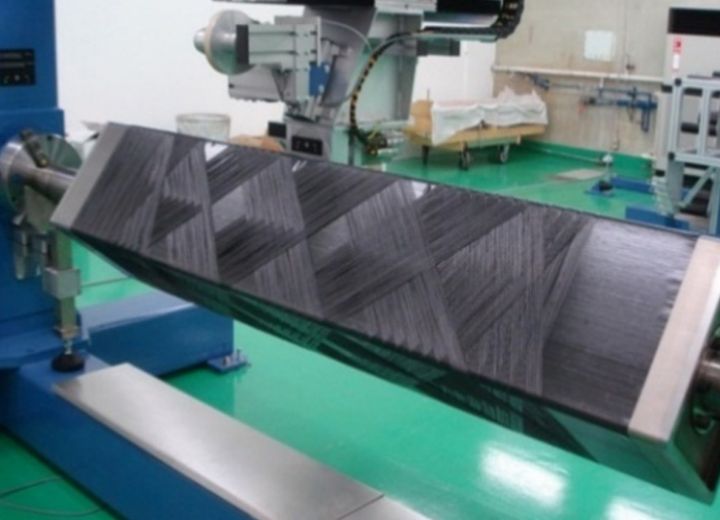
FWマシン
化学強化ガラスの製造技術
基材となるフロートガラスを自社で化学処理し、化学強化ガラスを製造しています。
フロートガラスの曲げ加工
最大加工サイズ約1m×1m、曲げ深さ150mm(要相談)の電熱ガラス曲げ炉を有しております。
化学強化ガラスの製造
化学強化槽を自社設備として備えております。
最大サイズとして2000mm×1000mm×曲げ深さ400mmのガラスを処理可能です。
オートクレーブによるガラスの貼り合わせ
有効寸法Φ1950mm×L3200mm、最高温度400℃、最大圧力1.96MPaのオートクレーブを有しております。
中間膜を使用したガラスの貼り合わせの他、熱硬化・熱可塑プラスチックの加熱成形が可能です。
アクリル・ポリカ・ガラスへのコーティング技術
(1)ウェットコーティング
コーティング液を樹脂成形品にフローコート法でコーティング後、加熱および紫外線照射により硬化し、樹脂成形品に種々の機能を持たせることが可能です。主な例を挙げると、表面に傷付き易い樹脂製品(特にポリカーボネート)に耐摩耗性ハードコードを施工できます。3D成形体へのコーティングも可能です。
特徴
- 表面の高硬度化
- 耐摩耗性、耐擦過性の付与
- 耐有機溶剤性の付与
- 3D成形体へのコーティング
主な用途
- 車輛用カバー
- レーシングカー用窓
- モビリティ用風防
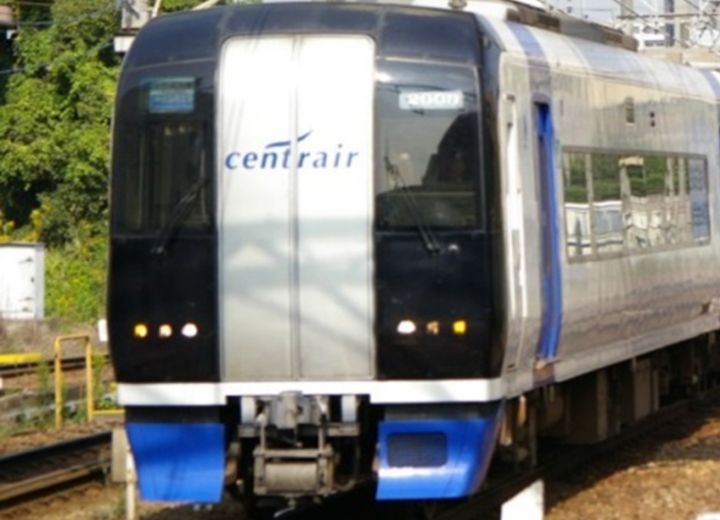
鉄道車両向け外板
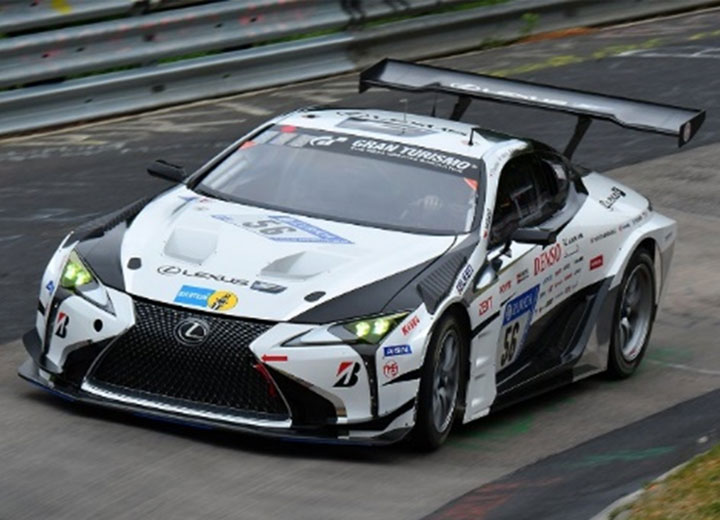
レーシングカー用の窓に施工
(2)ドライコーティング
アクリルやガラス表面にITO(酸化スズと酸化インジウムの混合物)を電子ビーム法又はスパッタリング法で成膜し、防曇・防氷機能、電磁波シールド性を付加することが可能です。透明樹脂(アクリル、ポリカーボネート)成形体、ガラス上への透明導電薄膜により付加価値をもたらします。
特徴
- 低抵抗ITO薄膜形成
- 高分子基材上への成膜
- 3D成形体上へのITO薄膜形成
主な用途
- 透明電極
- 電磁波シールド
- 発熱体
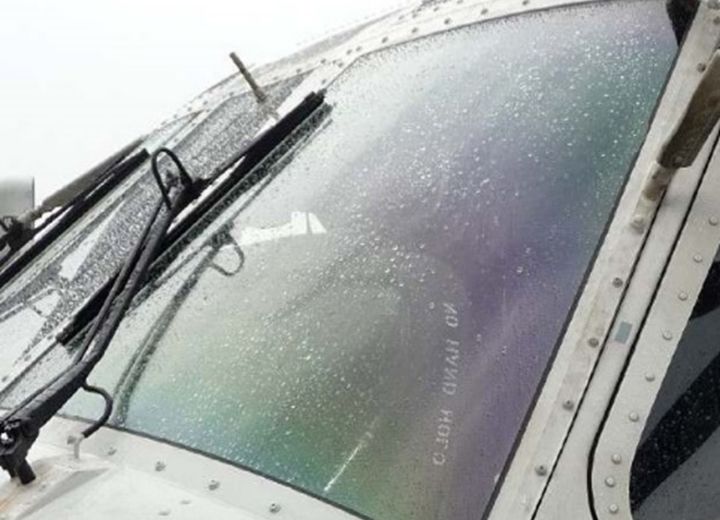
電熱機能を有した風防例
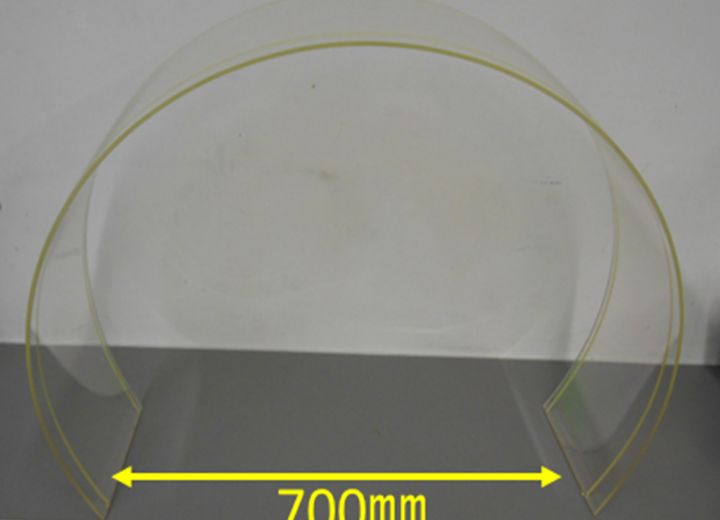
アクリル成型体への
ITO薄膜形成例(内側に形成)
対応力
多品種少量生産に対応
1985年にオートクレーブを導入し、30年以上にわたり、機体メーカーの加工外注として航空機で用いられる複合材部品の生産を行っております。
大型製品から試験片レベルまで対応したオートクレーブ成形を得意とし試作品等の単発ものから量産まで柔軟に対応しています。また、製作数量1個から生産することが可能です。

(複合材成形品の一部)
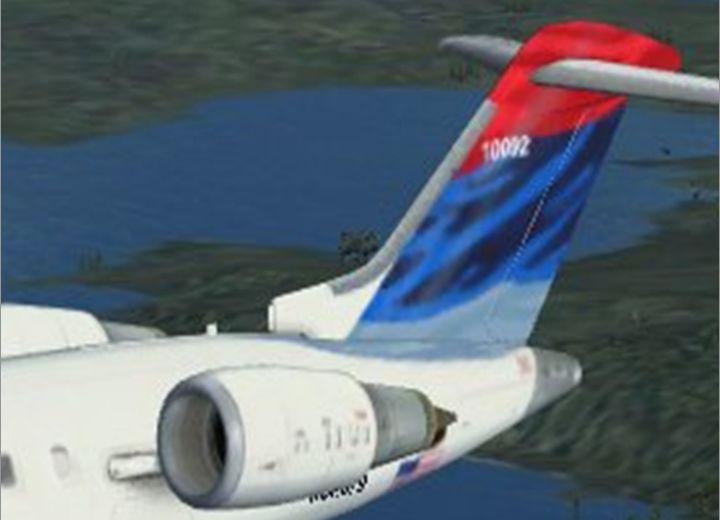
(複合材大型製品の例)
大型のアクリル・ポリカ製品が成形可能
高い光学特性を実現した曲げ加工技術で歪の無い大型のアクリル・ポリカ製品を成形することが可能です。列車の要求条件を満たす難燃性ポリカーボネートの成形や、加熱方法を工夫して成形を行い、直径2.4mのドームの製造実績があります。
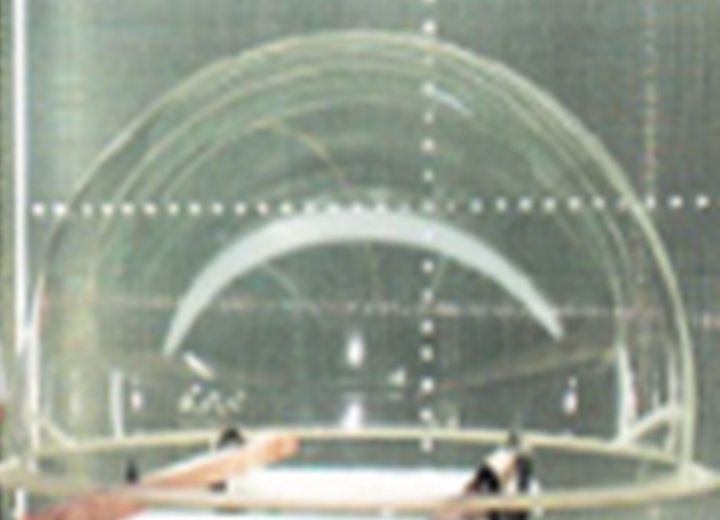
提案力
製造プロセスの提案
強度解析ソフトによる強度計算を行い、強度解析の結果に基づいた設計から部品製作までの製造プロセスをご提案します。
強度解析
積層仕様の強度解析を行い、破壊強度を予測します。
- CADデータからFEM構造強度解析に展開
- 強度解析結果から破壊強度/位置の予測
- 予測だけで無く、供試体の破壊試験による実測データの取得にも対応
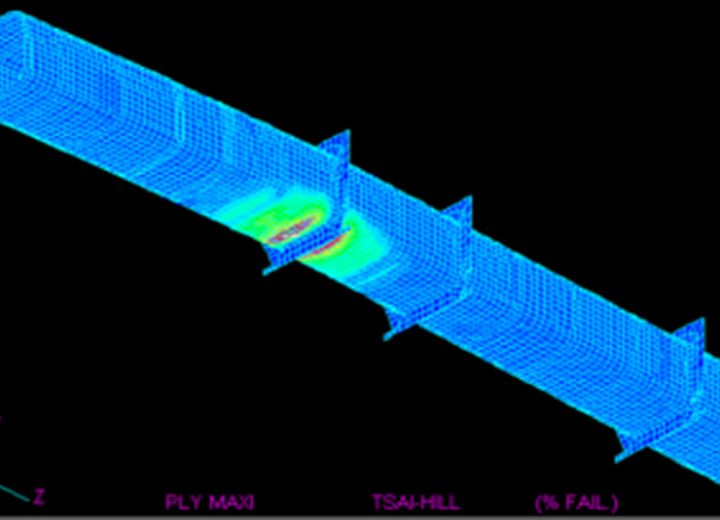
FEM強度解析の例
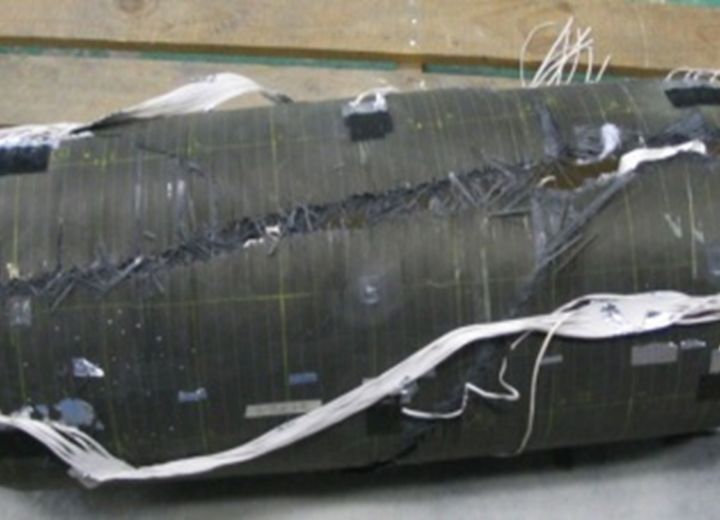
破壊試験に供されたCFRPサンプル品
成形シミュレーション解析
積層仕様の解析を行い最適な積層パターンを予測します。
- CADデータからプリプレグ切断形状に展開
- プリプレグ積層仕様からFW成形シミュレーション
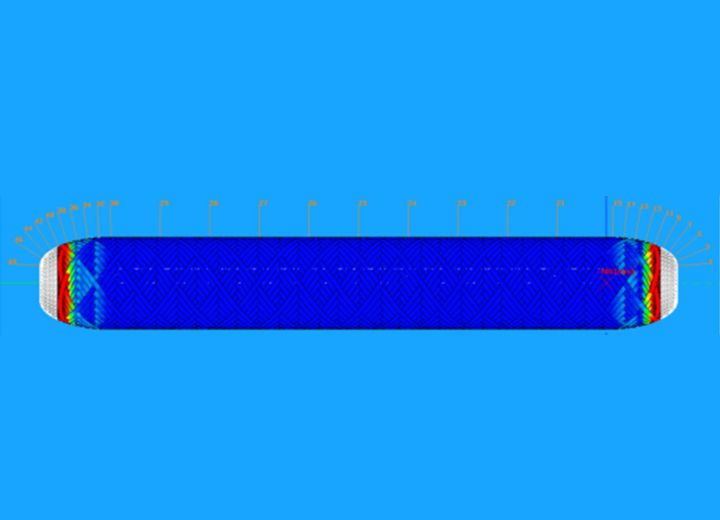
長尺タイプ製品:3500㎜
(マンドレル:4500㎜)
FW成形シミュレーション
最適な材料及び成形方法を提案
複合材部品の軽量・複雑形状の製造技術を保有しており、最適な材料で最適な成形加工方法を提案します。これまでに培った経験と製造技術により、強化繊維CF(カーボン)、GF(ガラス)、AF(アラミド)繊維と各種熱硬化又は熱可塑性樹脂と組み合せた材料を用いた部品の成形加工を得意としております。
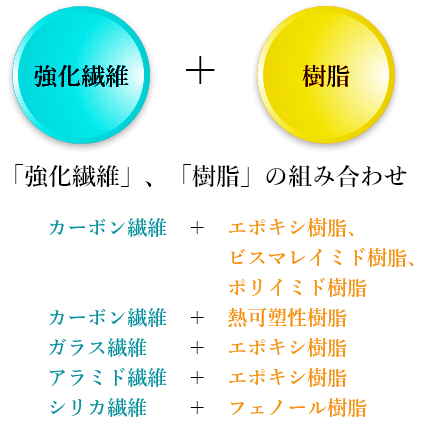